The potential and ability of EPS foam formwork on a finished concrete product is nearly unmatched.
The time- and labor-efficient process that creates unique designs and shapes in concrete is a game-changer when it comes to bringing ideas to life, letting them stand out, and ultimately withstand the test of time.
At Scott System, our team is able to manufacture complex foam shapes and design details that will facilitate the creation of structural and decorative concrete.
Whether it’s unique architectural designs, difficult double-curved surfaces, or any design that cannot utilize traditional forming methods, foam formwork design is a lightweight and cost-effective solution when compared to steel and wood alternatives.
Working with an experienced formwork expert who collaborates with architects, engineers, and contractors will develop the best results.
Best Uses for Foam Formwork
Using expanded polystyrene (EPS) foam formwork in an architectural concrete project can save companies time and money.
Unlike wood or steel, there is limited setup and removal time foam formwork, as well as fewer truckloads of supplies and less labor associated with the process.
Foam formwork will also not warp or distort while on the worksite unlike its counterparts. Choose from a variety of final surface coatings to get a smooth or textured finish that could also be reused throughout the project.
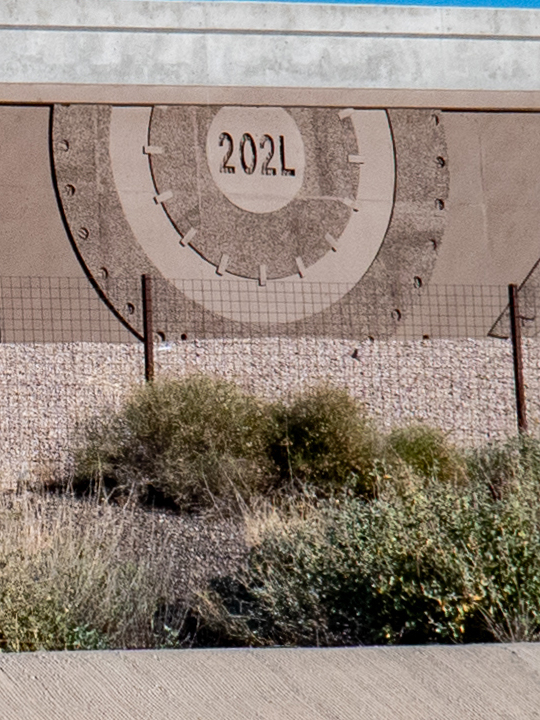
Lindsay Road (Maricopa County SR 202L)
The murals were created by utilizing 6 different Scott System standard textures including #171 Crushed Stone, #159 Split Face Rock, #177 Random Stone, #111 Stone Fractured Granite, #154 Sine Wave and Smooth.
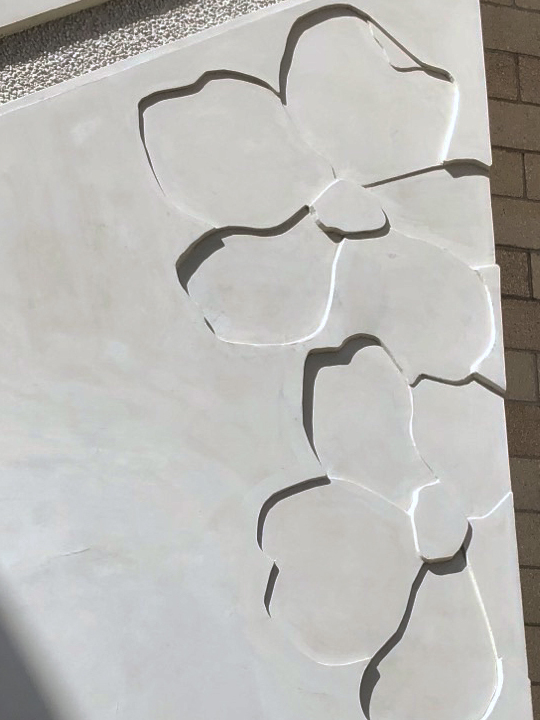
Kihei High School “Water Feature”
In early 2022, we began working with Nordic PCL Construction, based out of Honolulu, HI, on the Kihei High School “Water Feature”.
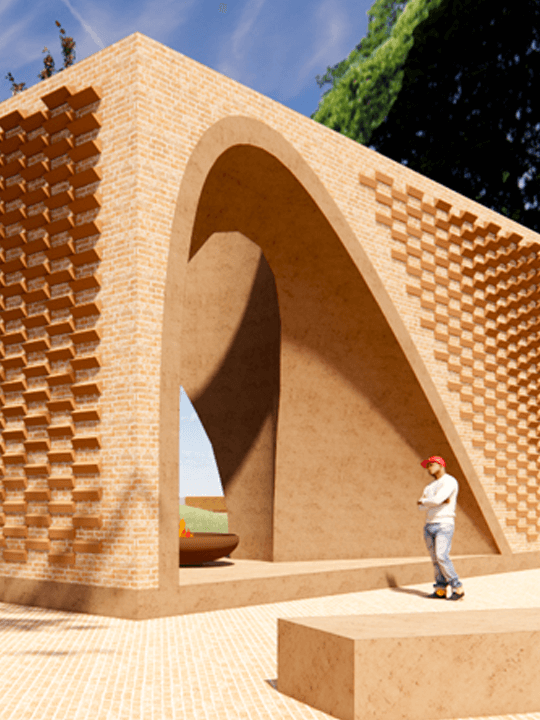
Memorial to the Enslaved at the College of William & Mary
The Memorial to the Enslaved, located on the William & Mary Campus was constructed to commemorate and honor the men, women, and children once enslaved by the college.
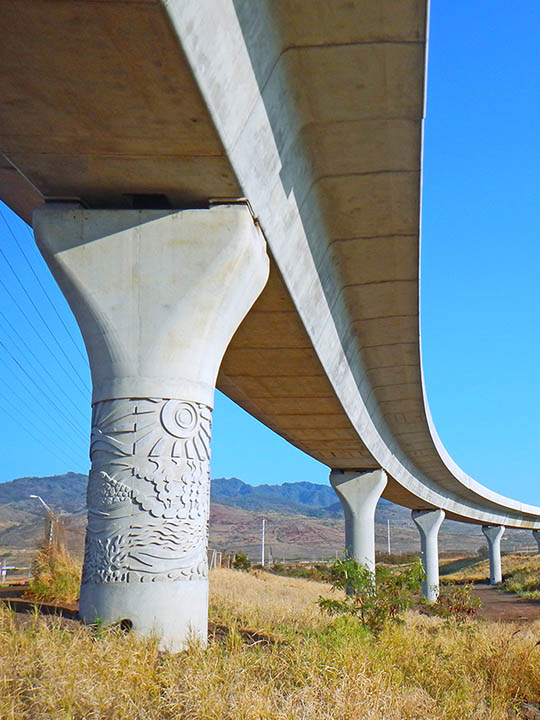
Honolulu Rail Transit Columns, Hawaii
The Honolulu Rail Transit Project (also known as the Honolulu High-Capacity Transit Corridor Project) is a light metro system under construction in Honolulu County, Hawaii, U.S.
Our Foam Formwork Process
Scott System will work with your team from start to completion to create a finished product ready for the job site.
Our engineers will create custom plans and create high resolution design files for your approval. Next, we will use our CNC milling capabilities to create the desired shape and fulfill the order with a parts test fit and final assembly ready for delivery.
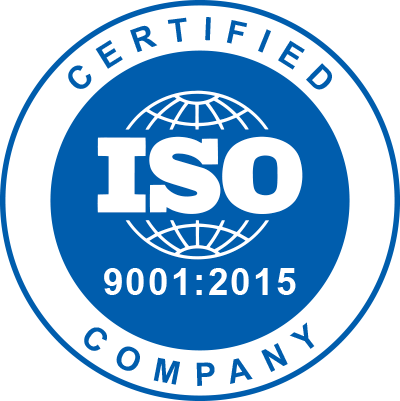
Why Scott System?
Certified Company
Scott System is ISO 9001 certified, employing a structured procedure to ensure our clients receive products that are held to stringent quality standards.
Client Support
You will always get a team member on the phone and will never have to talk to a machine.
Approval Process
Each job is kicked off with a detailed approval package including drawings and CAD files to ensure we know exactly what is needed for the project.
Quality Service
We are not happy until you are.
We will be a part of your project until it is 100% complete and not just when the parts leave our site.
Partnerships
Through the combined efforts of our precast and metal fabrication sister companies, we can provide a range of packages to the construction industry.